9. Bearing lubrication
Найти дистрибьютора
9.1 Types of lubrication
Oil or grease are used under normal conditions for bearing lubrication, or in special cases solid lubricant is used, e.g. for extreme temperatures or operation in a vacuum. When deciding on the type and method of lubrication, one must consider the operating conditions, the characteristic properties of applied lubricant, the design of the equipment, and its operating efficiency. Oil lubrication provides better lubrication characteristics, but grease lubricants make for easier use in bearings.A comparison between oil and grease lubrication is provided in table 9.1.
grease lubrication | oil lubrication |
low temperatures | high and extremely low temperatures |
low speeds (65% to 85% of revolutions, which can be achieved during oil lubrication) | high rotational speed |
protection against entry of contaminants (glands, covers) | oil seals to prevent leakage |
long-term maintenance-free operation | bearings are lubricated from a central source, which also serves to lubricate other machine components |
weak cooling | heat dissipation via oil circulation |
removal of contaminants from grease not possible | easy removal of particles from lubricant using oil filter |
9.2 Grease lubrication
Under normal conditions, most of the loadings use grease lubrication. An advantage of grease is that it holds better in the loading, it seals the housing against entry of contaminants, moisture, and water and, in particular, affords easier bearing maintenance.
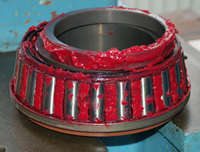
Fig. 9.1
9.2.1 Composition of grease lubricants
- Base oil – most frequently a mineral-based or synthetic oil. Lubrication properties of the grease are usually given by the properties of the base oil. Base oil viscosity is the decisive factor when selecting grease. Greases produced from low-viscosity base oil are suitable for high speed and low temperature applications, and lubricants with high-viscosity base oil are preferred for high temperature and heavy load applications.
- Thickening agent – the type of thickening agent, in particular, affects the grease dropping point and determines the application for a particular operating temperature; the higher the dropping point, the higher the temperature resistance of the grease. The maximum operating temperature of grease however is affected by the thermal resistance of the base oil. The water resistance of grease depends solely on the type of thickening agent.
- Additives – greases often contain additives that enhance certain grease characteristics or extend its life. Among the most commonly used are antioxidants (extend life), corrosion inhibitors (improve corrosion resistance), and EP additives (extreme loads).
9.2.2 Basic grease characteristics
- Base oil viscosity – the grease viscosity is given by the base oil; it is the most important factor when selecting a grease and has the most significant effect on the thickness of the lubricating film in the contact area and hence the bearing life. The oil viscosity is defined as the measure of flow resistance during lubricant sheer stress. The viscosity increases exponentially proportionally to the pressure and exponentially decreases proportionally to the temperature.
- Characteristics of captured oil – grease assumes all characteristics of the base oil, such as viscosity, freezing point, and flash point; such characteristics significantly influence the behaviour of grease.
- Consistency – greases are divided into several consistency classes according to the NLGI (National Lubricating Grease Institute) classification. The grease consistency should dramatically change within the temperature range and during mechanical loading. If an unsuitable grease consistency is selected for a given loading, then the grease may leak out of the bearing or may increase the rotation resistance and lead to insufficient oil release in the contact area.
9.2.3 Miscibility
An overview of roller bearing grease is provided in table 9.2.
Grease characteristics for roller bearings | ||||
Grease type | Characteristics | |||
Thickening agent | Base oil | Heat range of use [°C] | Water resistance | Application |
Lithium soap | mineral | -20 to 130 | resistant | multi-purpose lubricant |
calcium soap | mineral | -20 to 50 | highly resistant | good sealing effect against water |
sodium soap | mineral | -20 to 100 | non-resistant | emulsifies with water |
aluminium soap | mineral | -20 to 70 | resistant | good sealing effect against water |
lithium complex soap | mineral | -20 to 150 | resistant | multi-purpose lubricant |
calcium complex soap | mineral | -30 to 130 | highly resistant | multi-purpose high temperature, high-load lubricant |
sodium complex soap | mineral | -20 to 130 | resistant | suitable for high temperatures, high loads |
aluminium complex soap | mineral | -20 to 150 | resistant | suitable for high temperatures, high loads |
barium complex soap | mineral | -30 to 140 | resistant | suitable for high temperatures, high loads |
bentonite | mineral | -20 to 150 | resistant | suitable for high temperatures and low speeds |
polycarbamide | mineral | -20 to 160 | resistant | suitable for high temperatures and medium speeds |
lithium soap | silicone | -40 to 170 | highly resistant | suitable for wide temperature ranges and medium rotational speeds |
barium complex soap | ester | -60 to 140 | resistant | suitable for high temperatures and high speeds |
9.2.4 Amount of lubricant
- ½ to ⅔ free space at speeds below 50% bearing limiting speeds.
- ⅓ up to ½ free space at speeds above 50% bearing limiting speeds.
Bearings operating at very low speeds, as well as the free loading space, should be fully packed with grease to protect the bearing against corrosion and entry of contaminants.
9.2.5 Re-lubrication
Bearings must be re-lubricated if the expected bearing life is longer than the uptime of the applied grease. The re-lubrication interval is significantly influenced by the type and size of the bearing, the operating speed and temperature, and by the type and quality of grease.
The re-lubrication interval is the period during which the grease possesses the required lubricating characteristics. After this period elapses, the bearing must be re-lubricated after thoroughly first removing the old grease from the bearing space. The recommended re-lubrication intervals for individual types of bearings under normal load (P ≤ 0.15 C) and normal operating conditions is provided in the diagrams on figures 9.2 and 9.3. The diagrams apply for common greases for temperatures up to +70°C. At temperatures above +70°C, the re-lubrication intervals are reduced to one-half their original values for every increase of 15°C. At temperatures below 40°C, the re-lubrication intervals may be increased two-fold.
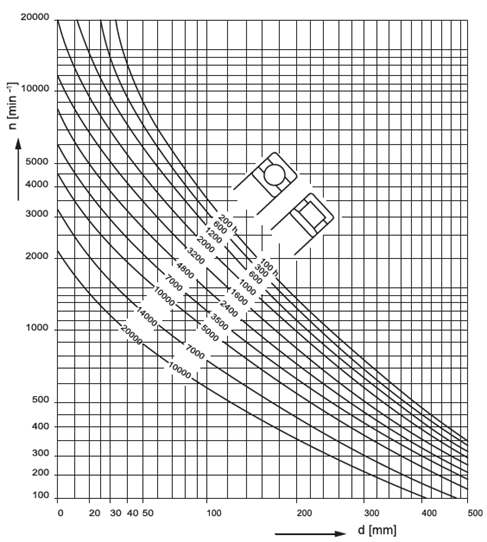
Fig. 9.2
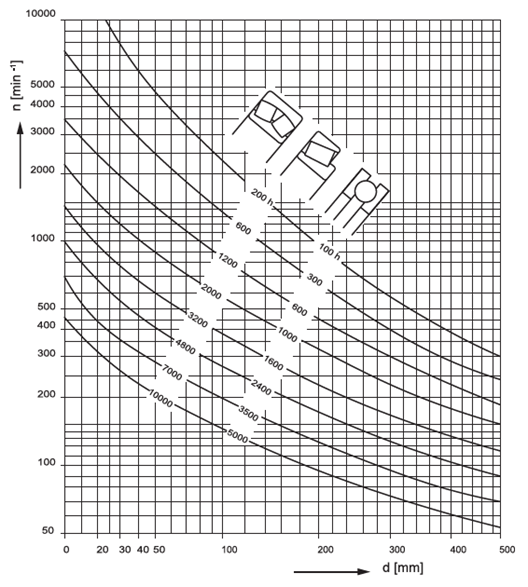
Fig. 9.3
The grease should be re-packed whenever the re-lubrication interval is longer than 6 months. The re-lubrication intervals may be greater when using extreme performance grease. More information will be provided by the ZKL Technical and Consultation Services Department.
The amount of grease required for re-lubrication can be calculated from the equation
Q=0,005*D*B [g]
Q – quantity of grease [g]
D – outer bearing diameter [mm]
B – bearing width [mm]
Used grease should first be removed from the bearing space in high-speed bearings, requiring more frequent re-lubrication. This helps to prevent any undesired rise in operating temperatures. A grease slinger can be used to prevent bearing over-lubrication. It comprises a plate, which rotates on a shaft and the centrifugal force pushes out any excess and degraded grease through the slot in the housing out of the bearing (fig. 9.4).
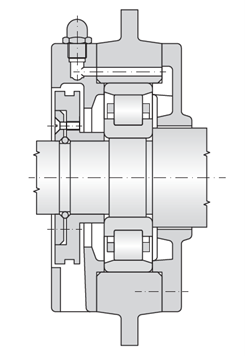
Fig. 9.4
- Vibrations – kneading of grease occurs during large vibrations and shocks, requiring more frequent re-lubrication. If grease becomes soft, grease with higher mechanical stability or stiffer grease must be used.
- Vertical shaft – the re-lubrication interval must be shortened by half and requires the use of glands and covers that prevent the leakage of grease from the loading.
- Contamination of grease – the re-lubrication intervals must be shortened, when the grease contains undesired particles, which can have a negative effect on the bearing life.
9.3 Oil lubrication
Oil lubrication is used when the rotation speeds are so high that the grease re-lubrication periods are too short. Another reason may be the need to dissipate heat from the bearing or when the temperature of the environment is high, which prevents the use of grease or if adjacent components already use an oil lubrication design (e.g. gearbox gears). With the exception of select spherical-roller bearings, such loadings are always lubricated with oil.The use of oil lubrication necessitates that lubrication during running in and afterwards, during operation, be ensured. Excessive use of oil increases the oil temperature and thus the bearing temperature. The oil supply to the bearing is secured using various design methods:
- Oil bath lubrication – the most popular and simplest method of oil lubrication for low and medium rotational speeds. The oil level extends to the centre of the bottom rolling element and must be maintained at this level. The oil is carried by the rotating components of the bearing and dispersed in the bearing to return to the oil bath.
- Circulating oil lubrication – used most often in high speed applications, where the bearing needs to be cooled and for high temperature applications. Oiling is achieved by a pump. After the oil passes through the bearing, the oil is fed back into the sump, re-filtered, and cooled, as needed.
- Drop lubrication – is widely used for lubrication small ball bearings used in high speed applications.
- Oil splash lubrication – oil is splashed on the bearing by a rotating gear wheel or by a simple rotor adjacent to the bearing. The bearing does not need to be immersed in the oil bath; this method of lubrication is often used in automobile transmissions.
- Oil injection lubrication – generally used for high-speed bearings. Oil is injected under pressure directly into the bearing. The oil jet velocity must be sufficiently high to ensure that the oil penetrates through the swirling air created by the rotating parts of the bearing.
- Oil mist lubrication – injects an oil mist into the bearing. This method of lubrication is often used for lubricating spindle bearings of machining centres.
- Oil-air lubrication system – compressed air is used to supply a very small, precise amount of oil into each bearing to ensure sufficient lubrication and to better achieve lower operating temperatures and higher speeds. This lubrication method is used for lubrication most spindle bearings and for other high-speed applications.
9.3.1 Oil lubricants
Certain types of bearings, e.g. spherical-roller bearings, spherical-roller thrust bearings, or tapered roller bearings usually achieve higher operating temperatures than other types such as, e.g. ball bearings or roller bearings under identical operating conditions. This must also be considered when selecting the type of oil.
The decisive characteristic of oil is its kinematic viscosity, which decreases as the temperature increases. We can determine the appropriate oil viscosity from the diagram on fig. 5.4 in relation to the mean bearing diameter ds = (d+D)/2 and the rotating speed.
If the operating temperature is known or can be identified, a suitable oil and viscosity on fig. 5.5 can be determined using the internationally standardized reference temperature of 40°C, required for calculating the χ ratio. Figures can be found in chapter 5 Determining the bearing size.
The use of oil with EP additives is recommended when the χ ratio < 1, since they increase the oil film bearing capacity. Oil with EP additives must always be used, whenever the χ value falls below 0.4. Improved reliability of the respective loading design is achieved if χ > 1.
Example:
- bearing: d = 180 mm, D = 320 mm, ds = 250 mm
- rotation speed n= 500 min-1
- expected operating temperature 60°C
ν1 = 17 mm2s-1.
Adjusting for an operating temperature of 60°C, the applied oil, selected according to the diagram on fig. 24 at a standardized temperature of 40°C, must have a minimum kinematic viscosity of 35 mm2s-1.
The kinematic viscosity of lubricating oil for spherical-roller thrust bearings is estimated according to table 9.3 relative to the product n*d, where n is the bearing rotation speed in revolutions per minute and d is the bore diameter in mm. Lower viscosity values apply for low-load bearings, for which the relationship Pa ≤ 0.1 Ca applies. Higher values apply for Pa > 0.1 Ca.
Oil viscosity for spherical-roller thrust bearings | |
d*n | kinematic viscosity of oil [mm2s-1 at 40°C] |
1 000 | 250 to 550 |
10 000 | 100 to 250 |
100 000 | 45 to 100 |
200 000 | 30 to 80 |
9.3.2 Changing oil
9.4 Lubrication using solid lubricants
Sold lubricants are used for lubricating bearings only in cases, when grease or oil are unable to meet the demands for reliable lubrication under limiting friction conditions or when required to provide adequate resistance against high operating temperatures, chemicals, and similar other effects.Graphite, MoS2, and PTFE, in particular, are used for bearing lubrication. The lubricating mechanism is given by the lattice structure of compounds; the layers of particles easily slide along each other and adhere well to a metal surface, which prevents the displacement of lubricant particles during sliding or rolling motions.
Drawbacks of solid lubricants:
- High coefficient of friction
- Inability to act as a coolant
- Limited uptime
- Low dampening of vibrational instability of rolling elements and cage